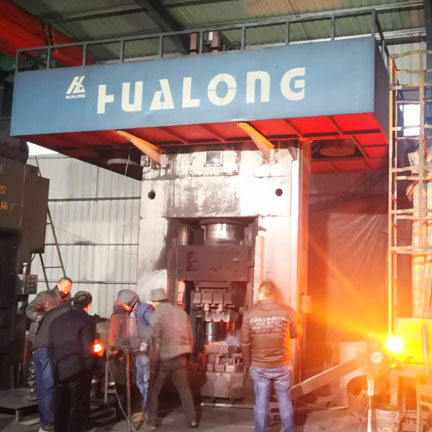
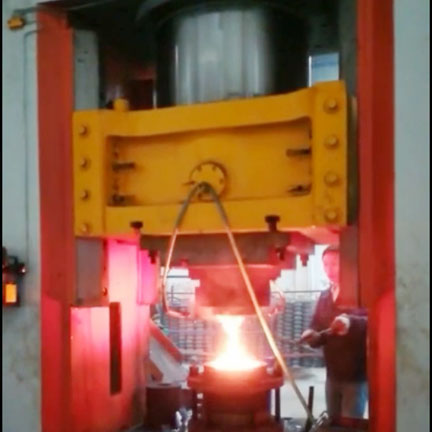
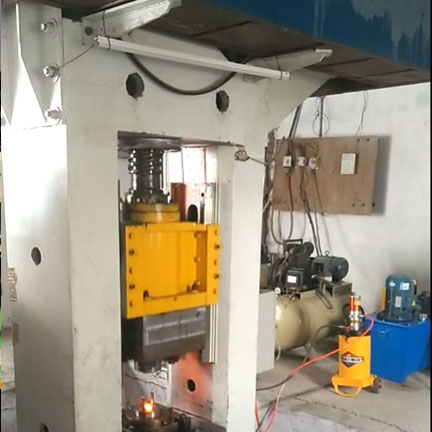
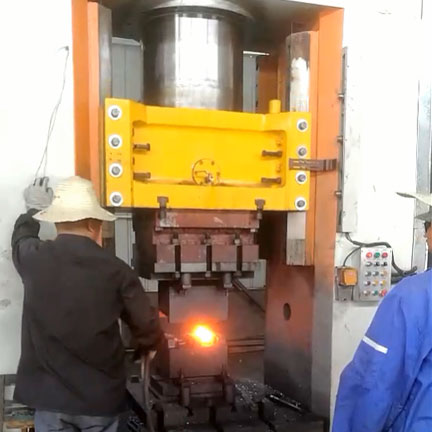
hot forging presses machine
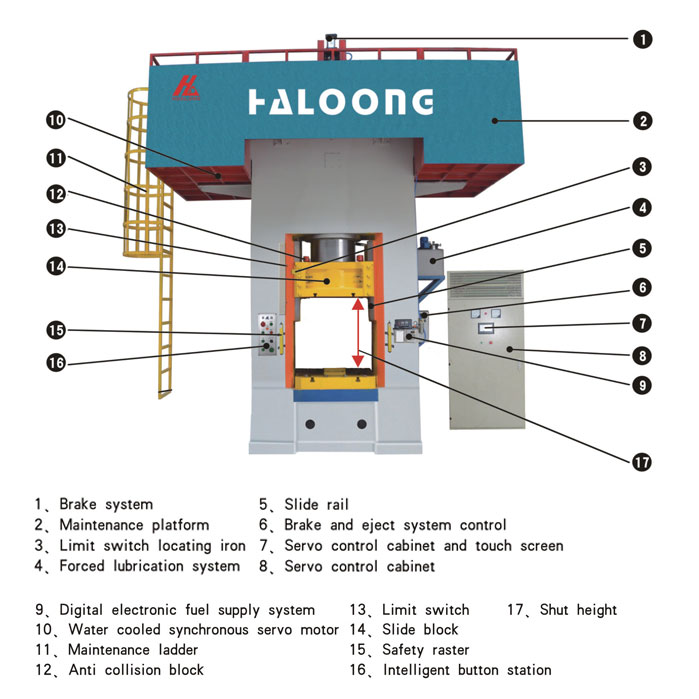
Product Description:
Haloong press machine were equipment with servo motor,electric oil feeding system,damping design,touching screen,safty grating.Haloong electric screw press is designed for producing various types of metal wares. The press machine is also named as power screw press, forging / forge press, cold press, stamping press and punching machine. After replacing a proper mold,this electric screw press machine can also producing various refractory bricks. Therefore, the press machine can be named as hot die forging press or hot molding press
By introducing of the world's advanced technology, our company developed HLDS Series Forging Press. HLDS Series Hot Forging Press is widely used in areas of : auto parts,machinery parts,hardware,agricultural machinery parts,toothed gear,automobile, tractors, internal combustion machinery,ship, aviation, mineral machinery, petroleum machinery, hardwares and tools.also used in the forging and precise trimming of bulk ferrous and non-ferrous metals.
Features of HLDS series CNC servo press:
1.precision control ,quick response
The pressure can be exactly set in advance, every process can be made repeatedly and precisely , which ensure the products to be homogenized. Servo motor is direct drive without clutch, so it can response quickly.
2.Reasonable structure,homogrenized products
Due to reasonable sesign of structure, can't worry about the overload caused by overload caused by oversize or uneven heating, and slip jam ( or seizure caused by overload).While for the same material, the different repeated pressures can be used to make ti gradually deformed and successsively forged. For the machines with bottom dead point, it has to be considered the unevenness of forged parts caused by bottom dead point moving when pressurizing .
3.Quick forming , extend die's lifetime
The speed of slide block will be very quick when it nears to the bottom dead point , so the time is very short to forming the material, and the forged parts can be completed before it becomes cool. However crank press or toggle press is used for hot forge, the forging time is longer, the tempreture of die is very high and it has to be cooled by water.In general,for hot forge, the shorter time of forging, the longer lifetime of die.
4.Simple structure, cheaper maintenance
The serov motor is direct drive, and it has simole structure and less components, so its maintenance cost is very cheap. For normal operation, there is no need for other brakes, the servo motor itself can make slide block to stop. The mechanical brake is only for the second protection when power off, so the lifetime of brake is extremely long.
5.Process controlled as planned, wide application range.
According to set pressure energy, the servo press can make slide block fall down acceleratedly first, then slow down the slide block, and press the forged parts with set energy, the press with bigger tons can forge small parts, one stroke time is little change,The bigger press can be used to instead smaller press ,and the bigger one can yield twice the result than that of smaller one.
6.High efficlency,reduce the production cost.
The servo motor runs only at forming process, but the friction motor need fun continuously. Compared with friction press , the servo press can save 55% energy.
7.Stamp forming, high energy
The pressurization is the same as that of friction press,the servo press is instant shock pressurized, the pressure energy is very high. For the same forge, the crank press with 1.3-1.8times nominal pressure should be used.
8.LOWER noise and vibration
Compare with impact hammer, the pressure of servo press produces inside of the frame, there is no excessive vibration to the ground, so the cost fo foundation is cheaper.The noise and vibration of servo press are far less than those of impact hammer.
9.High automation unmanned production
The automatic production line is available,and the whole automatic process do not need the skilled workers.
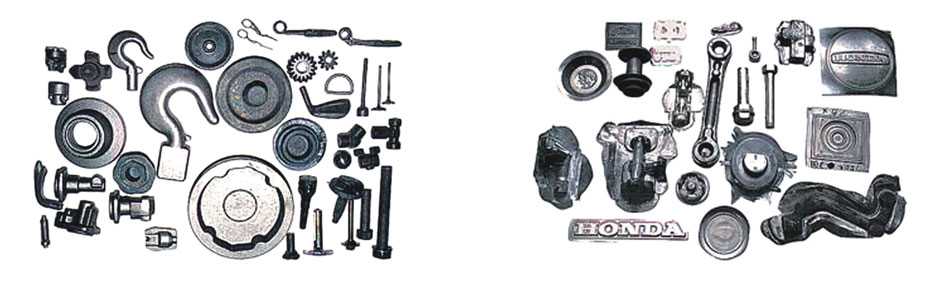
Model | Nominal pressure | Max. | Slide stroke | stroke | Die set height | workatable size | overall size | Motor | Weight |
(KN/T) | pressure | (mm) | No. | (mm) | (mm) | (mm) | (Kw) | (T) | |
(KN) | (mm) | ||||||||
200F | 2000/200 | 4000 | 650 | 30 | 1000 | 900×660 | 2600*1600*4481 | 22 | 10 |
315F | 3150/315 | 6300 | 650 | 28 | 1100 | 1200×880 | 3150*2100*5500 | 37 | 21.5 |
400F | 4000/400 | 8000 | 700 | 28 | 1250 | 1200x1050 | 3300*2200*5500 | 50 | 26 |
630F | 6300/630 | 12000 | 750 | 26 | 1440 | 1250x1050 | 4000*2640*6500 | 84 | 52 |
1000F | 10000/1000 | 20000 | 700 | 22 | 1255 | 1350x1100 | 5600*2640*6600 | 2*78 | 75 |
1200F | 12000/1200 | 24000 | 700 | 22 | 1255 | 1450x1100 | 5600*2640*6600 | 2*84 | 78 |
1600F | 16000/1600 | 32000 | 800 | 20 | 1370 | 1800x1460 | 6200*3300*7300 | 2*136 | 118 |
2000F | 20000/2000 | 40000 | 800 | 18 | 1370 | 1900x1460 | 6500*3500*7600 | 2*160 | 157 |