Comparison between servo press and mechanical press in flexi
Author: haloong Time: 2018-08-09 10:27:57
With more and more extensive application of stamping process in automobile, electronic information, electrical machinery, instruments, ships, aerospace, national defense and other industries, as well as more and more serious and urgent problems of energy and environment, the energy saving in the production process has also been put on the agenda, while the energy consumption of press is the main energy consumption. It is reported that there are more than 1 million press machines in China at present, most of them are ordinary mechanical press, and their computational energy efficiency is only about 20%. According to the average 20kW/ unit calculation, the electrical power wasted exceeds 1.600 * 107kW, and the annual energy wasted is nearly 80 billion kilowatt.
Energy saving in manufacturing industry is the key to reduce energy consumption per unit of GDP. Stamping processing is an important part of the manufacturing process. Unadjustable "rigid" drive mode is the main reason of low efficiency of traditional forming equipment. The fundamental way to save energy is to change rigid power into controllable "flexible" power, with controllable speed, adjustable capacity, and energy recovery.
Forming process curve chart
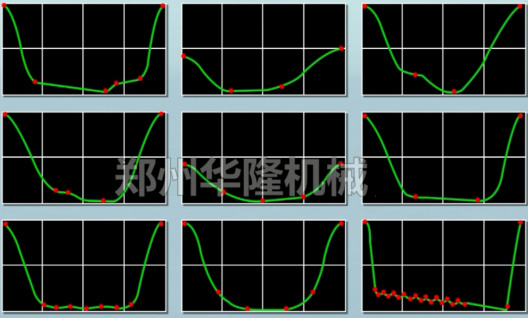
More forming processes can be realized by servo electric screw press
In general pressure machines, where the SPH value is increased by the flexibility of the servo electric screw press, the motor load is relatively stable. Even in the non-working period of the working cycle, the flywheel will consume energy to restore the speed of the flywheel. For AC servo drive, without the flywheel, the actual power consumed is variable. As far as the rated power of the motor is concerned, the servo electric screw press will be larger than the ordinary mechanical press. However, the actual energy consumption of the servo electric screw press is still lower than that of the normal press because the power consumption of the two drive modes is quite different.
Process can be optimized by using the servo electric screw press technology, for some molds and parts size, reasonably adjust parts mould height, stroke by adjusting the parts so that the output per hour can improve to a certain level, in accordance with production targets stamping servo line annual production of about 900000 pieces of processing time from the original 5000 h to 4285 h, can save 750 h labor and electricity costs, increase the income of 1.0405 million yuan annually.
At the same time, the servo electric screw press has the characteristics of compound, high efficiency, high precision, high flexibility and low noise environment protection, which makes its application in the forming process more important. The technology of servo electric screw press can be optimized and has great flexibility. There is a wide variety of slider movement curve, by adjusting the mould cushion blank-holder force of different position, improve the parts formability compared with sub-contractor to reduce the scrap rate of the parts, improve the quality of the surface of the parts, reduce the repair rate, improved the qualified rate of parts of an offline, save part repair fee $202848 a year.
Ac servo drive can not only improve the working performance, automation and intelligence, but also realize the great energy saving of the press, which is the development direction of forming equipment. The flexible application of servo electric screw press also improves the utilization rate of raw materials and expands the possibility of new materials.